High-performance punching of longitudinal frame members at HÖRMANN Automotive
Longitudinal frame members form the backbone of any commercial vehicle. These components have very vehicle-specific geometric designs. ‘That’s because the pattern of holes used for attaching the various add-on parts can vary depending on the customer, industry or trim level of the truck,’ explained project manager Alexander Duschka. ‘That means that it’s not unusual to see a batch size of one, but we also handle batches of more than 100 on a daily basis,’ added Lothar Becker, managing director of the company’s factory in Gustavsburg.
This presents a lot of challenges for the manufacturing process because it is necessary to accommodate the wide range of variants while maintaining a high degree of automation and keeping takt times low so that the components can be produced at competitive prices. HÖRMANN Automotive has been running a fully integrated production line for manufacturing longitudinal frame members since 1999. The customised hole patterns are created by means of hydraulic CNC punching machines. However, the punching process has always been something of a bottleneck in the process chain because every one of the holes, which can number as many as 800 per member, has to be made individually. Consequently, two parallel punching systems were integrated when the overall line was set up, with a third added in 2006. Despite that, it was never possible to make the most of the potential inherent in the highly productive forming process in particular because punching was slowing down the entire process.
In 2017, an interdisciplinary team from HÖRMANN Automotive saw an opportunity to unlock this potential by working on a technology – one of a kind anywhere in the world – that would make it possible to clear the bottleneck. The company joined forces with a supplier to refine the team’s vision, resulting in a punching system that went into operation in 2019. Investing in this innovation laid the foundations for almost doubling the output of the forming line and turning that had previously been a bottleneck into a pacesetter. Combining the old and new punching systems made it possible to achieve a takt time of less than a minute for creating an entire hole pattern.
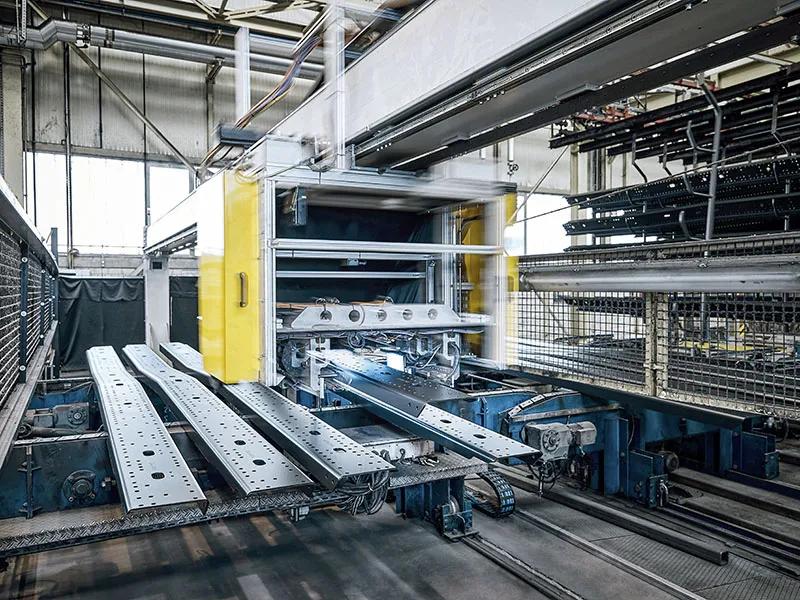