HÖRMANN Automotive opens new painting system for high-quality coatings
HÖRMANN Automotive Eislingen GmbH has begun operations with a new power coating system at its factory in Ebersbach. ‘This system is used to pre-treat workpieces and assemblies of fuel tanks, panels and flaps as well as heating ducts for buses and similarly sophisticated components in a multi-stage wet chemical process and then to coat them with powder paint in a manual or automated booth,’ explained Tobias Frenzel, managing director of HÖRMANN Automotive Eislingen GmbH.
What makes the new painting system special is that it can coat parts measuring up to 2.7 metres long, 2.0 metres tall and 1.3 metres wide. It can also coat steel and aluminium substrates simultaneously. The whole process requires only limited personnel and is very flexible in terms of the range of parts it can incorporate. ‘In a diverse customer landscape, we have secured an established position for ourselves as a reliable supplier,’ said technical manager Rudolf Ostwald. ‘Whether it’s small fuel filler flaps for buses, large steel or aluminium tanks for cranes and tipper trucks or panels for agricultural and construction machinery, HÖRMANN Automotive in Ebersbach will now be able to carry out all powder coating and painting work in-house. That will cut delivery times for our customers by quite some margin and will reduce the risk of quality defects.’
However, those are not the only improvements that can be expected now that the powder coating system is operational. Production processes will be streamlined, less time and effort will be spent transporting goods and working conditions will be improved.
High coating and surface quality
Once they have left the loading station, which is essentially the gateway to the painting system, the components go through one of two four-chamber pre-treatment systems depending on whether they are made of aluminium or steel. After drying, the parts are cooled in a dust-free room. That prevents tiny unwanted particles from adhering to the surface, which could result in paint defects. The parts are then taken to a cleanroom, which is even better protected against dust than the previous room. This contains a manual powder booth and an automated powder booth. These are used to coat the components with powder.
After coating comes a two-line gelling and powder enamelling furnace. In this area, the components are not exposed directly to hot air but are initially merely pre-heated to cure the powder on the components. In the subsequent furnace section, the powder enamelling furnace is used to enamel the applied powder at temperatures of up to 230 C.
Additional technology and a wider product range
The installation of the new painting system is also an example of companies within HÖRMANN Group working in harmony. The rough technical concept was devised by employees in Ebersbach working closely with experts and consultants. Factory planners from HÖRMANN Rawema supervised the implementation of the project. The factory in Ebersbach will also be offering up its new capabilities in surface coating to other HÖRMANN Automotive facilities, thereby broadening the range of technologies available.
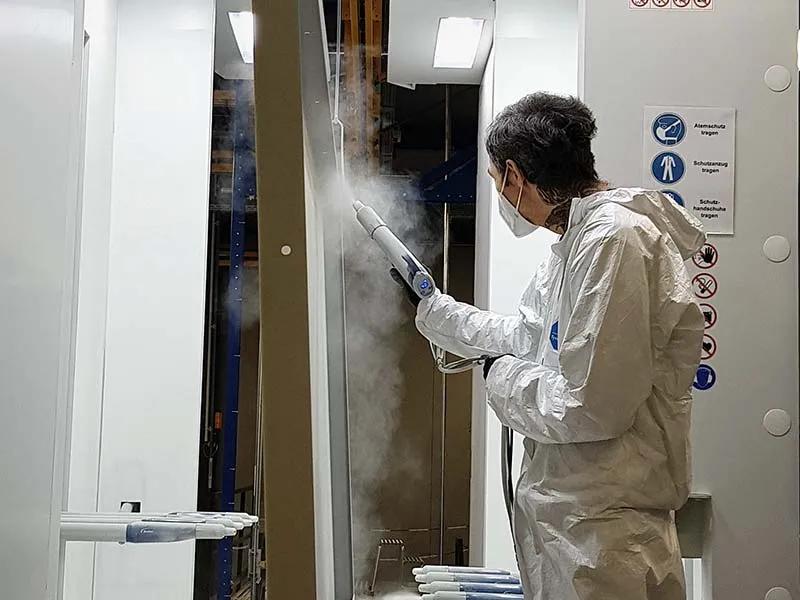
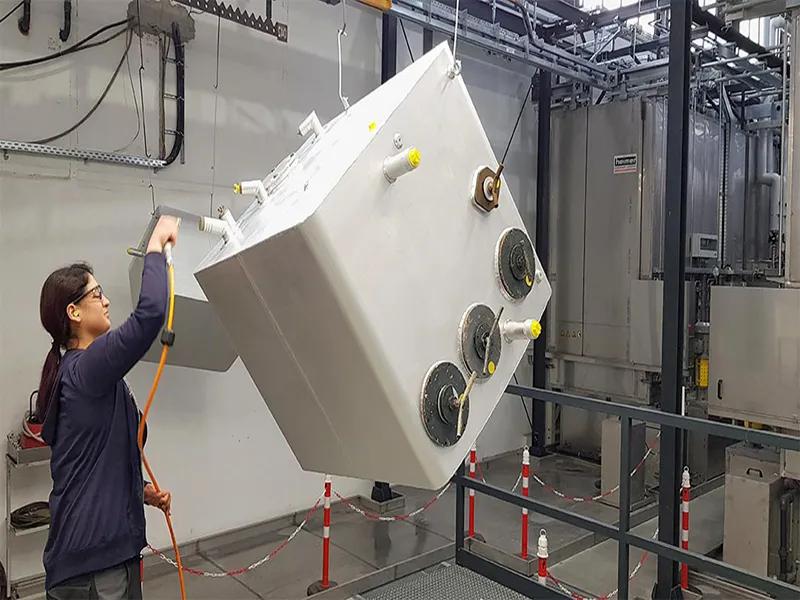
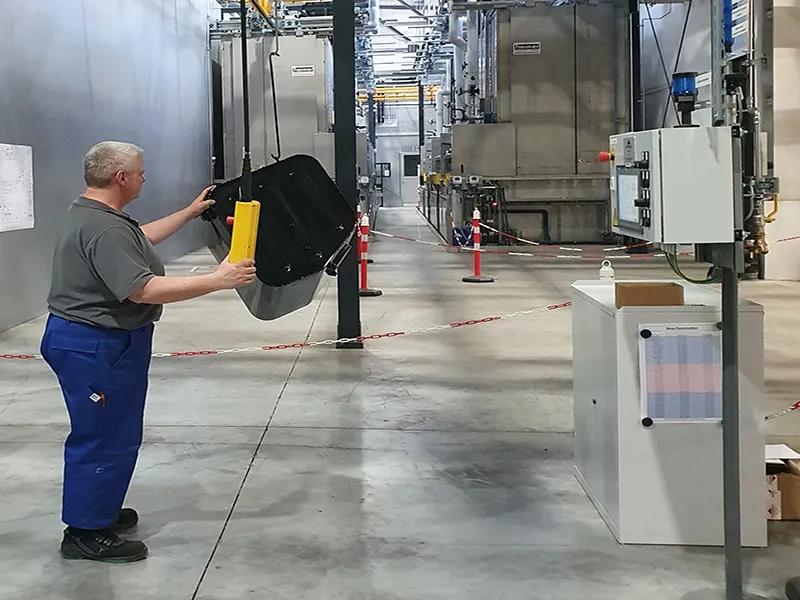