HÖRMANN Industrieservice improves takt time to boost productivity
HÖRMANN Industrieservice GmbH improved takt time at an OEM’s assembly facility and optimised the workplace while taking ergonomic and environmental factors into account. The company worked with the customer to devise a plan that would improve the loading and unloading of two adjacent machines used to process components.
The components first had to be placed into each machine via loading gantries. Loading and unloading had to take place one after the other: first machine 1, then back to the start, then machine 2. Once it had unloaded, each loading gantry had to travel empty back to the component retrieval station so that it could pick up another part. While this was happening, the machine was not able to carry on processing a component because it had no component to process, which led to a lot of downtime.
This operation is now carried out by two robots that are able to load both machines in a staggered process. The distance that needs to be travelled has been reduced because the swing radius from component retrieval to loading is smaller. The components can now be transported simultaneously and alongside each other. There is no waiting time any more. ‘With the new system, we shortened distances and cut costs incurred as a result of machine and operator downtime, with as much as a threefold improvement in operation time,’ said Dirk Jakobs, managing director of HÖRMANN Industrieservice.
Good reputation resulting in follow-up projects
‘The customer assigned the project to us not only for financial reasons, but also on account of our experience and appreciative testimonials from other customers in the field of automation,’ added Jakobs. Another point in the company’s favour was that there were no problems with compatibility, because HÖRMANN Industrieservice was able to cover the entire project from A to Z, including planning, conceptual design, engineering design, data backup and automation, as well as mechanical and electrical systems. HÖRMANN employees were on hand throughout to make any necessary adjustments straight away.
Consequently, once the work was complete, the customer immediately commissioned the company for another project aimed at improving component manufacturing. The handling of the parts trays on the cockpit assembly lines, which contain components and are transported to logistics on assembly trolleys, will in future be taken on by robots. In the past, the trays were loaded by hand, often causing delays resulting in downtimes at final assembly. ‘The parts trays are now fully loaded to suit the vehicle in question in a just-in-time process at the assembly lines,’ said Jakobs.
All-in-one service for a trouble-free process
Employees from HÖRMANN Industrieservice designed and manufactured the gripper equipment for the robots. A Robcad analysis was used to determine the positions of the robots and the new working area. Once planning was complete, assembly and installation took place, involving robot control panels, power supplies and utility connections, lighting, wiring, pneumatics and grippers.
A steel maintenance platform was made specifically for the customer and fitted with an access point, steps, railings and safety equipment as well as photoelectric sensor equipment. This was followed by the process of programming and commissioning the robots and matching the internal robot interfaces to the system. ‘We generally supervise production for several weeks so that we can rectify any problems immediately and give the system operator hands-on training,’ said Jakobs.
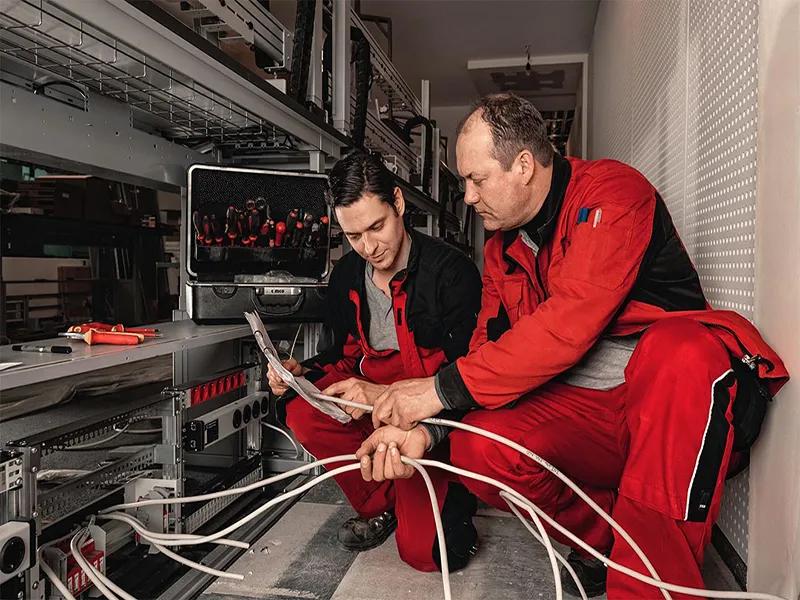