HÖRMANN Logistik commissions AutoStore® small-parts warehouse for Richter+Frenzel
Richter+Frenzel (R+F), a specialist wholesaler of plumbing and heating supplies, was setting up a logistics hub in Reichertshofen, a town near Ingolstadt, to be used to supply its branches and trade customers all over the country. A key aspect of this new-build project was a fully automated system for storing and gathering small parts. The team from HÖRMANN Logistik GmbH won R+F over with their intralogistics method. ‘Our concept for implementing the system centres on an AutoStore® small-parts warehouse. A conveyor system connected to it with integrated case erectors and sealers links the picking area to palletising and despatch,’ said Oliver Vujcic, managing director of HÖRMANN Logistik.
For the customised design of the AutoStore® system, HÖRMANN Logistik ran several real-time system simulations using original data during planning. This resulted in a system configuration with 45 robots, 50,000 containers over 16 levels and workstation modules to match. It also produced a recommendation to use multi-order batch picking. ‘With batch picking, the HiLIS AS warehouse management system gathers special orders into batches so as to achieve the maximum possible multi-order rate,’ explained Vujcic. HiLIS AS refers to HÖRMANN’s AutoStore® intralogistics system software.
Robots co-operating in a self-learning system
The AutoStore® system comprises an aluminium grid system enclosed on all sides. In the grid system, there are stacks of 16 containers each standing directly on the warehouse floor. There is a rail system mounted above the stacks of containers, and battery-powered autonomous robots travel around using these rails. The robots co-operate to pick up containers, sort them and are in charge of supply and disposal for the workstation modules.
The maximum total weight of the containers is 35 kilograms, with a net load of roughly 30 kilograms. To fill the containers in a way that is optimised for volume, HÖRMANN Logistik implemented a self-learning system for weight and volume data. Only items of identical type and quality are assigned to each container subset. The new AutoStore® intralogistics system from HÖRMANN Logistik entered operation at R+F in June 2020.
Centralised management and control software
The HiLIS AS warehouse management system developed by HÖRMANN Logistik manages the contents of the containers as well as all picking processes. The robots use Wi-Fi to communicate with the AutoStore® controller, which assigns the shipment orders to the robots. At times when there are not many orders to be fulfilled, or if their battery capacity is low, the robots will automatically return themselves to their charging stations.
‘HiLIS AS makes the best possible use of the opportunities afforded by AutoStore® and acts as an interface between the AutoStore® controller and the customer’s primary IT system,’ said joint managing director Steffen Dieterich. He added, ‘The integrated picking and palletising robots also communicate with HiLIS AS.’
HÖRMANN Logistik is one of the leading sales partners and integrators for AutoStore® systems in the Germany/Austria/Switzerland region and CEE countries. In 2020, the Munich-based company was honoured with a TOP 100 innovation award in the category for companies with 51 to 200 employees in recognition of its ‘top management that encourages innovation.’
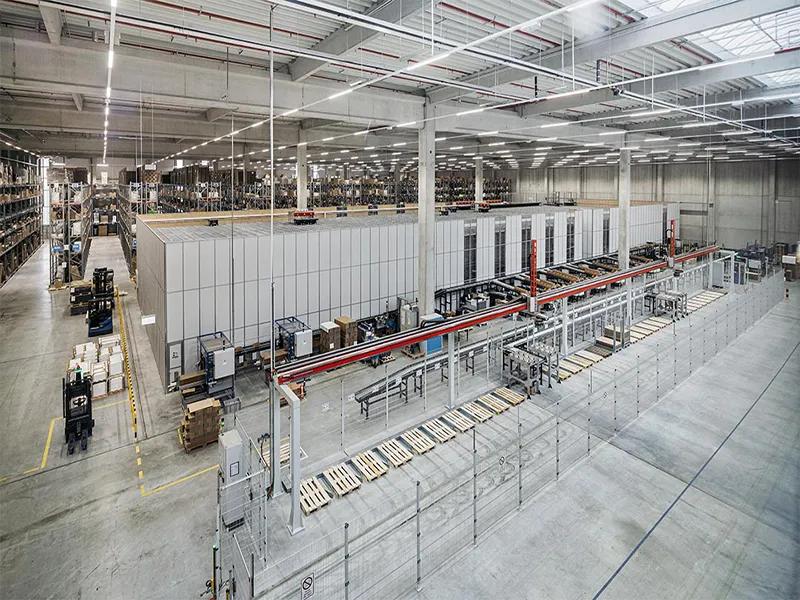
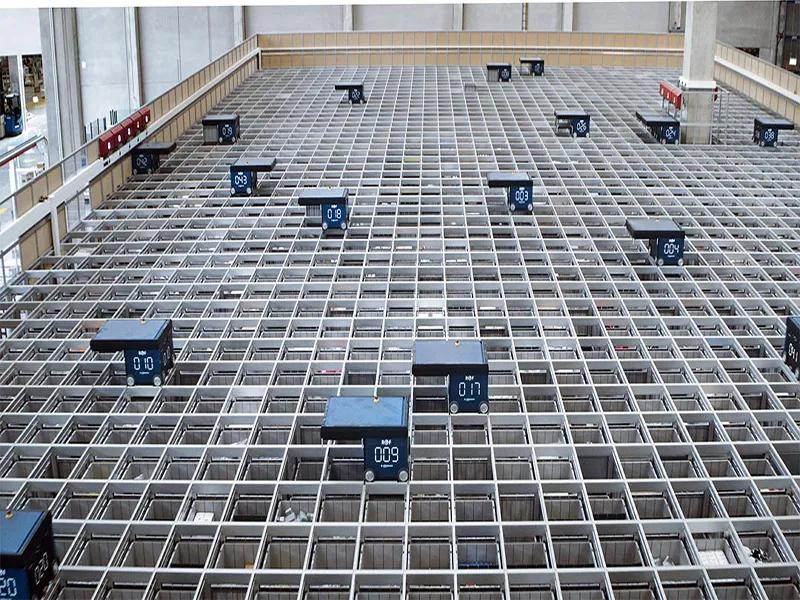
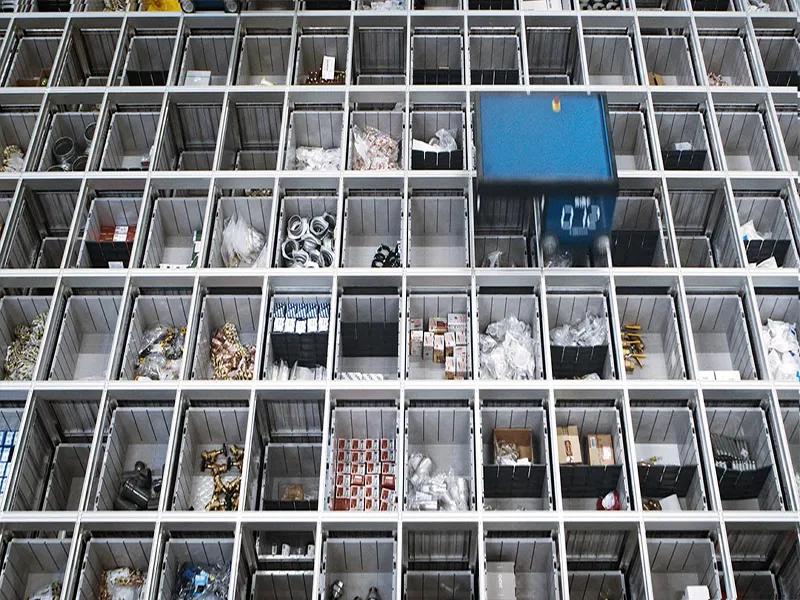