HÖRMANN Rawema using 3D technology for more efficient factory planning
For more than twenty years now, factory planners at HÖRMANN Rawema have been supporting Bharat Forge, the leading supplier of forged chassis and engine components, in its work relating to forming technology in forging in particular. How are the forging facilities set up? How much work is involved in building services engineering? Which automated process solutions are available? What are the requirements that the measuring equipment needs to meet? Finding answers to these questions is an ongoing process. ‘Above all, Bharat Forge relies on the expertise that stems from our wealth of experience, and we work together on efficient solutions to problems in areas ranging from system designs to product implementation,’ said Benjamin Bielefeld, innovation manager at HÖRMANN Rawema.
For several years, the most notable feature of this collaboration has been the consistent use of 3D planning. Because HÖRMANN Rawema always receives the data from a range of different sources in its capacity as lead designer, standardised interfaces are incorporated into planning alongside known data from established partners so as to offer customers planning that is tailor-made for them but is also reliable.
3D technology for more efficient factory planning
During the planning phase, HÖRMANN Rawema combines architectural data concerning elements such as beams and walls with data relating to building services equipment such as ventilation and air conditioning. These data streams can then be linked to the production facilities, for example. ‘All of this has to produce a consistent, efficient and functional structure at the planning stage, which means a lot of in-depth co-ordination between all involved,’ explained Bielefeld. The factory planners can then use the comprehensive 3D model to draw up timetables and plans for fine-tuning the details.
Once planning is complete, HÖRMANN Rawema uses the models for the implementation phase, working with suppliers to determine assembly sequences. Because many processes on a construction site take place successively, it is also necessary to have comprehensive on-site project management in place to keep things running as smoothly as possible. For longer modification projects, the factory planners have also been using 3D modelling with 3D laser scanning since 2015. These can also act as a starting point for digitalising existing structures.
The factory of the future
The work of a lead designer increasingly involves deploying all-encompassing 3D planning to make the planning process more accessible to customers and to allow more detailed conclusions to be drawn about the process. ‘Over the coming years, we are also going to be giving our customers the change to work with us to implement factory planning in virtual spaces,’ said Holger Füssel, managing director of HÖRMANN Rawema.
With this in mind, HÖRMANN Rawema is collaborating with a line-up of highly capable partners to refine its expertise in building information modelling (BIM), helping to draw up the VDI guideline for BIM factory planning, defining potential applications for augmented reality (AR) and virtual reality (VR) systems with a focus on collaborative working and also taking part in the AgilPlanBZ research project to investigate a flexible, adaptable factory for the production of fuel cells, with the goal of furthering the cause of efficient factory planning in an age of digitalisation in production. ‘Only by optimising the way we seize the opportunities presented by digitalisation we can identify future challenges at an early stage and thus deliver the best possible outcomes for our customers,’ said Füssel.
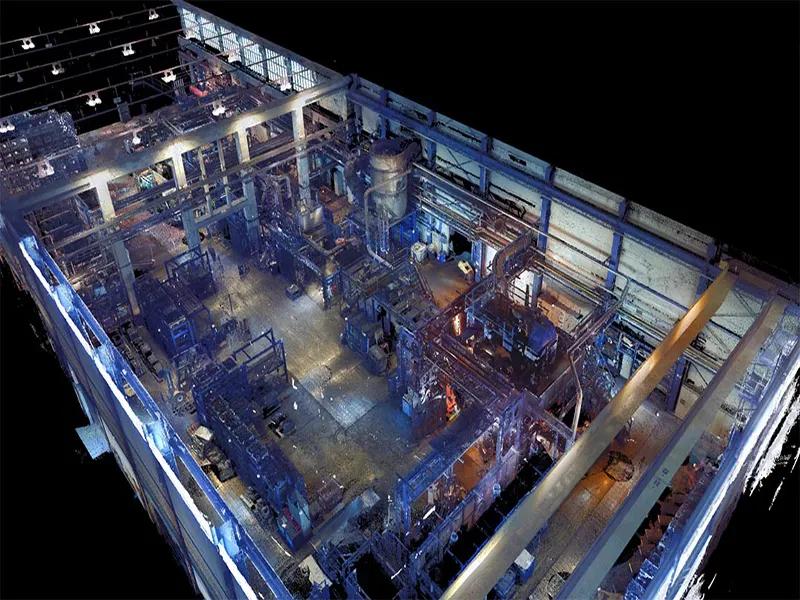
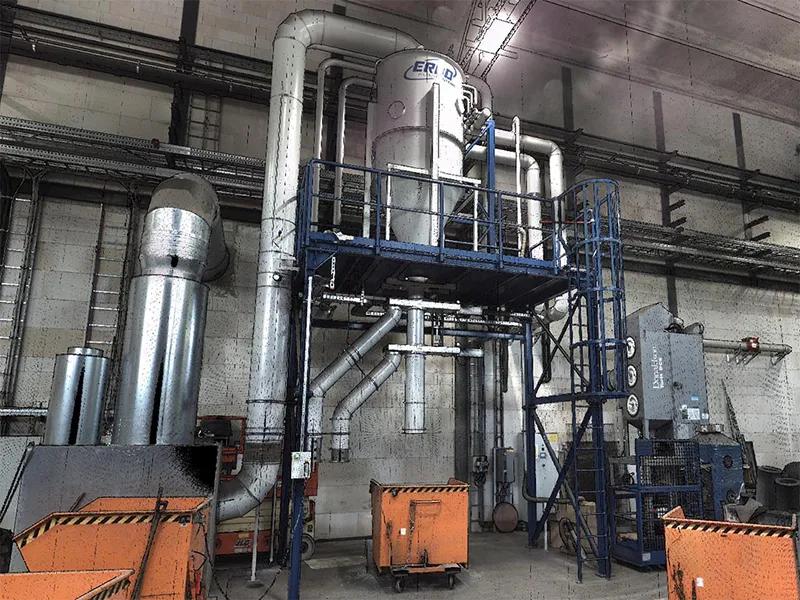