HÖRMANN Services offers automation of assembly lines for electric cars
The Services division is a highly specialist industrial service provider operating through its subsidiaries HÖRMANN Industrieservice GmbH, HÖRMANN Automationsservice GmbH and MAT Maschinentechnik GmbH. As a reputable partner to the automotive and mechanical engineering industries as well as various others, it handles a wide-ranging assortment of assignments in the life cycle of a production facility, from planning and project management to the assembly of machinery and installation of turnkey systems, as well as commissioning and condition-based maintenance.
The areas of expertise offered by HÖRMANN Services run the gamut of necessary services: mechanical design including steelwork; pneumatics and hydraulics; comprehensive planning of electrical distribution boards and digital networking; and programming of robots, including visualisation and documentation of the technical processes. With its experienced team of specialists, HÖRMANN Services also takes responsibility for the installation of new production facilities, as well as commissioning and assistance with the start of production.
One particular project in 2019 involved planning, installing and commissioning an entire fluid supply installation at an OEM’s assembly facility.
To cut the high costs associated with developing high-volume electric cars, the customer developed a new technology platform in the form of the MEB modular electric toolkit. Ensuring cost-effective manufacturing of large quantities of the steering components called for highly automated and digitally networked production facilities.
HÖRMANN Services lent the customer close support with the entire media supply installation for compressed air, cooling water and lubricants in the form of oil and grease, and also took responsibility for project management, covering procurement and commissioning including shift management during the start of production. Summed up in figures, the project involved installing 51 robot grippers, 633 cylinders, 550 single valves, 800 metres of fluid supply lines and cable trunking across roughly 1,600 square metres of space. The system entered operations after twelve months.
‘We are proud to have brought our specialist expertise and experience to bear in helping with the dynamic process of converting production systems in the automotive industry to make them suitable for electric vehicles,’ said managing director Gerhard Jacobi.
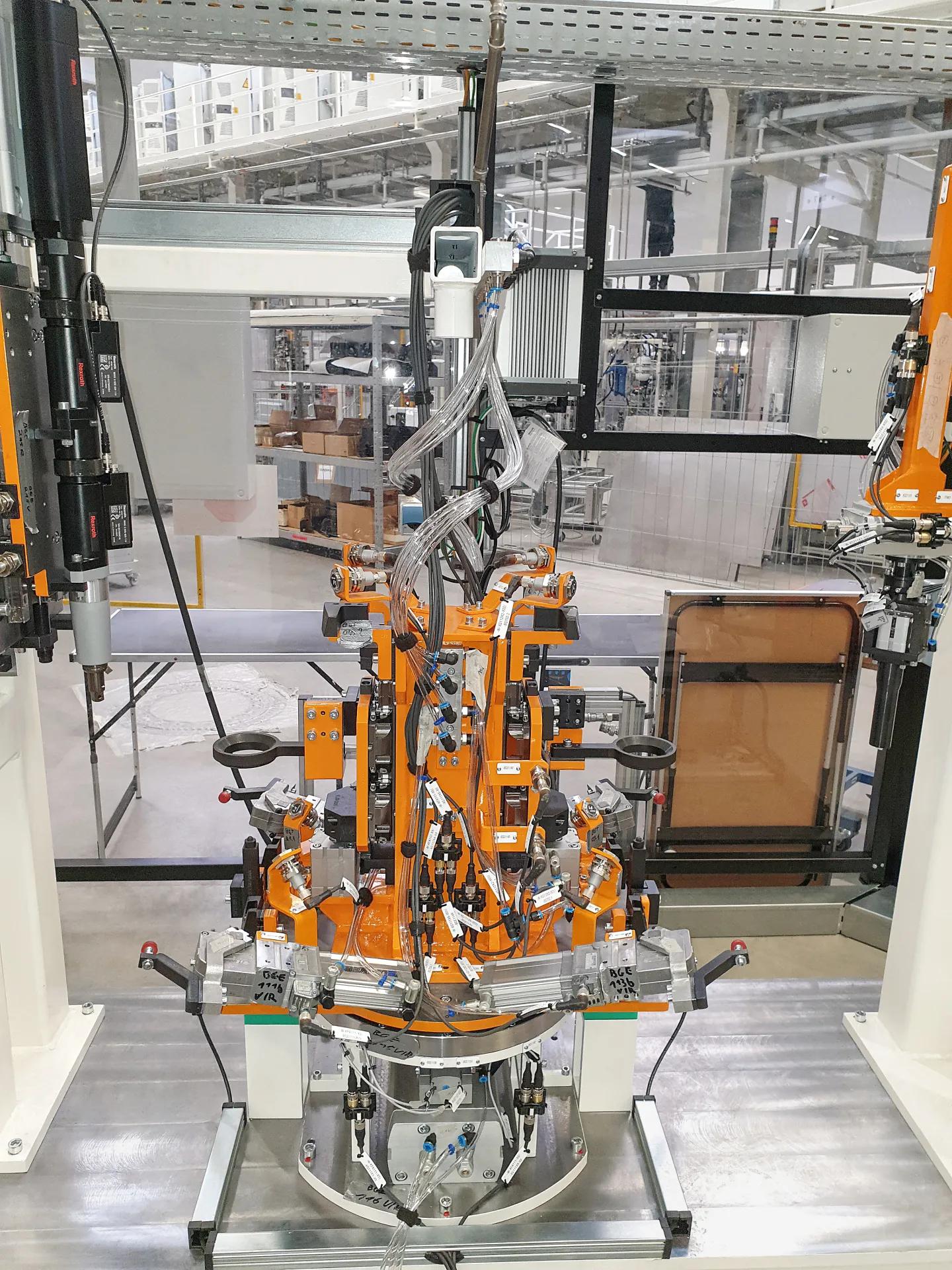
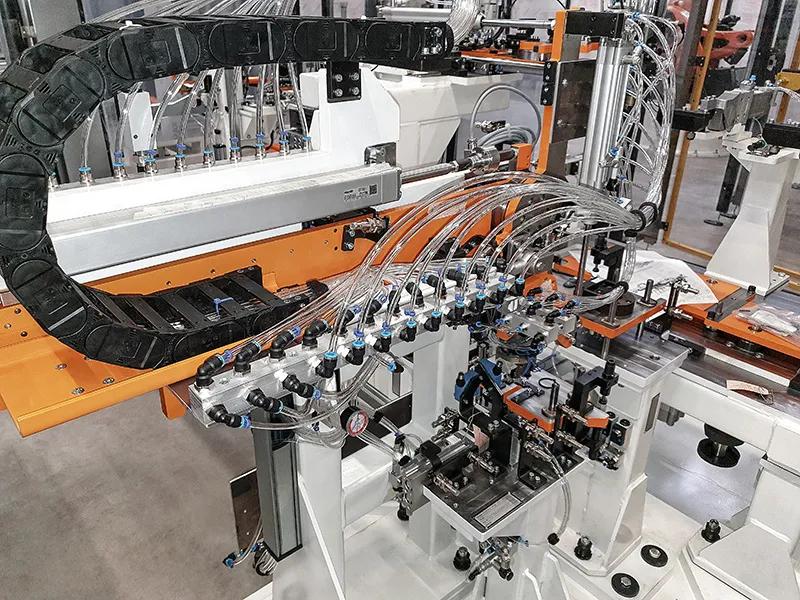