Innovative warehouse technology for the packaging industry from HÖRMANN Logistik
The ever-increasing popularity of online retail is leading to a boom in the corrugated cardboard and packaging industry, which calls for rapid and innovative solutions to the related logistical challenges.
At its Bad Neustadt site, Kunert Wellpappe was planning a new automated high-bay warehouse to clear space for additional production and to meet changing customer requirements for smaller order volumes with shorter delivery cycles and efficient inventory systems. The contract for implementing the new warehouse and associated conveyor system went to HÖRMANN Logistik. One special feature of the four-aisle shuttle racking system is the multi-deep sideways storage of a wide variety of finished goods in various shapes and sizes on different types of pallet, as well as on several sub-pallets.
Managing directors Steffen Dieterich and Oliver Vujcic explained, ‘A shuttle transports the packaging units from production to the handover point to the new conveyor system. As early as production, the system is already making sure that wherever possible, two identical packaging units are transported in succession so that they can then be conveyed, stored and retrieved in pairs once in the high-bay warehouse area. This improves the throughput of the warehouse by quite some margin. One packaging unit can have as many as six sub-pallets. Before they are deposited in the high-bay warehouse, all packaging units checked for length, width, height, pallet type and weight. The conveyor system then carries the packaging units to the pre-storage zone of the high-bay warehouse, where there is a pallet circuit featuring special chain conveyors and roller lift tables that connects the production, high-bay warehouse and despatch areas.
In the case of order-based retrieval, the HiLIS (HÖRMANN Intralogistics System) warehouse management system receives a retrieval order from the on-site HOST via an interface. The goods are retrieved by the stacker cranes and transported towards the despatch area by the conveyor system. There are various truck loading areas for both rear loading and side loading.
The unique challenge in the detailed planning and implementation of the new shuttle racking system at Kunert Wellpappe lay in the very diverse sizes and shapes involved as well as the large packaging units with several sub-pallets. In addition to the process of transporting these packaging units on a special conveyor system, some clever tricks of the trade were needed to allow the most flexible use possible of the large bays, optimised for volume. At around 42 metres, the height of the high-bay warehouse was also unusual. This height was the result of the limited space on the factory premises and the need to accommodate as many pallet storage bays as possible in the space available.’
HÖRMANN Logistik’s work on the project included racking steelwork; roofing and wall cladding including smoke and heat extraction systems; drainage and lightning protection; pallet conveyor systems for transporting packaging units from production and linking up with the high-bay warehouse, block storage and despatch; stacker cranes; fire doors and high-speed doors; rack sprinkler systems; and the HiLIS warehouse management system, including system visualisation. The project was approved and put into operation in 2019.
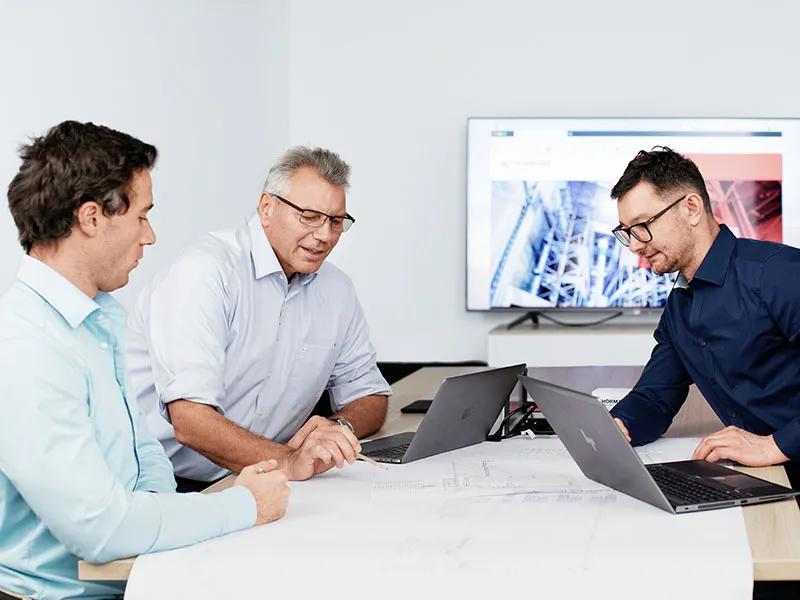
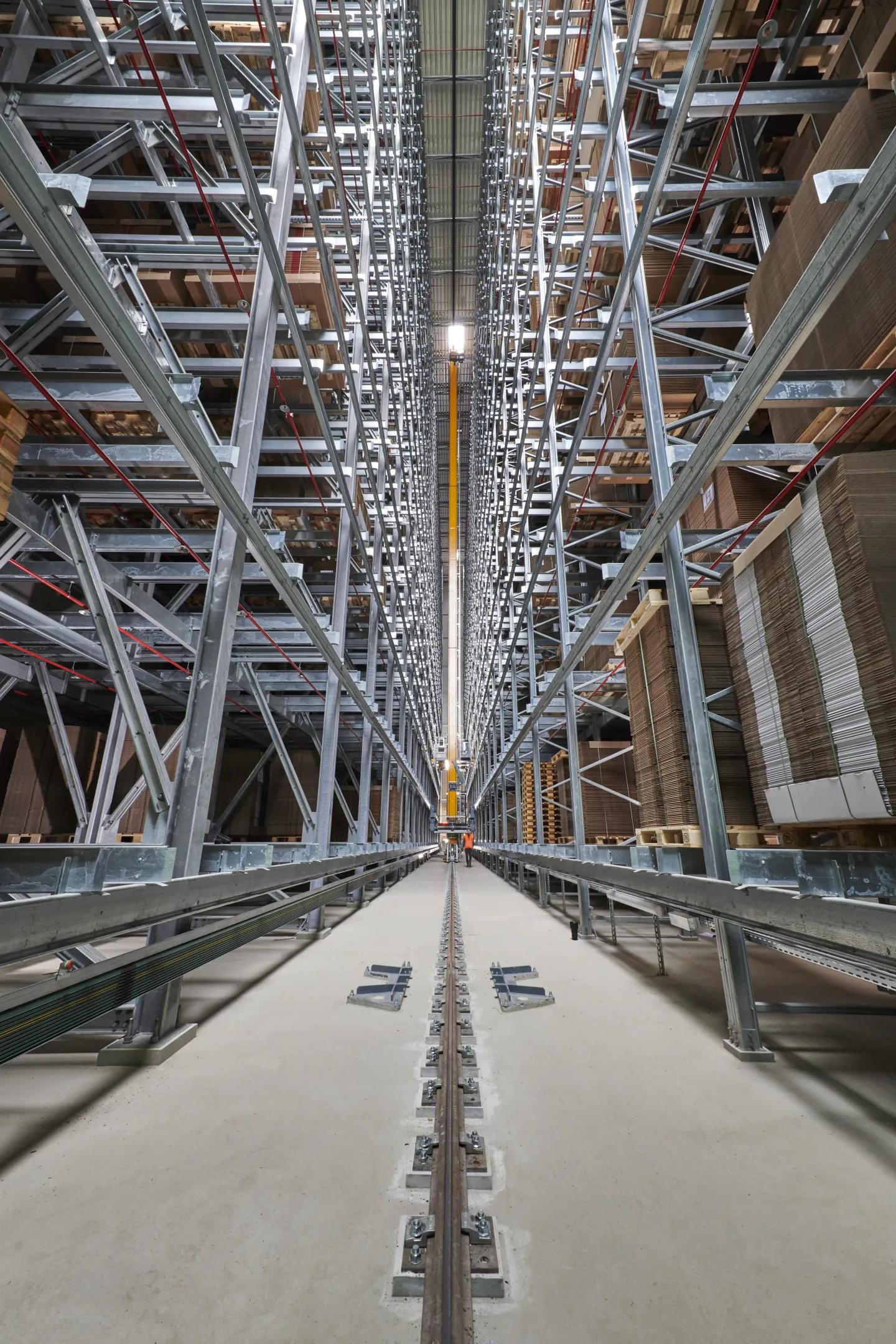