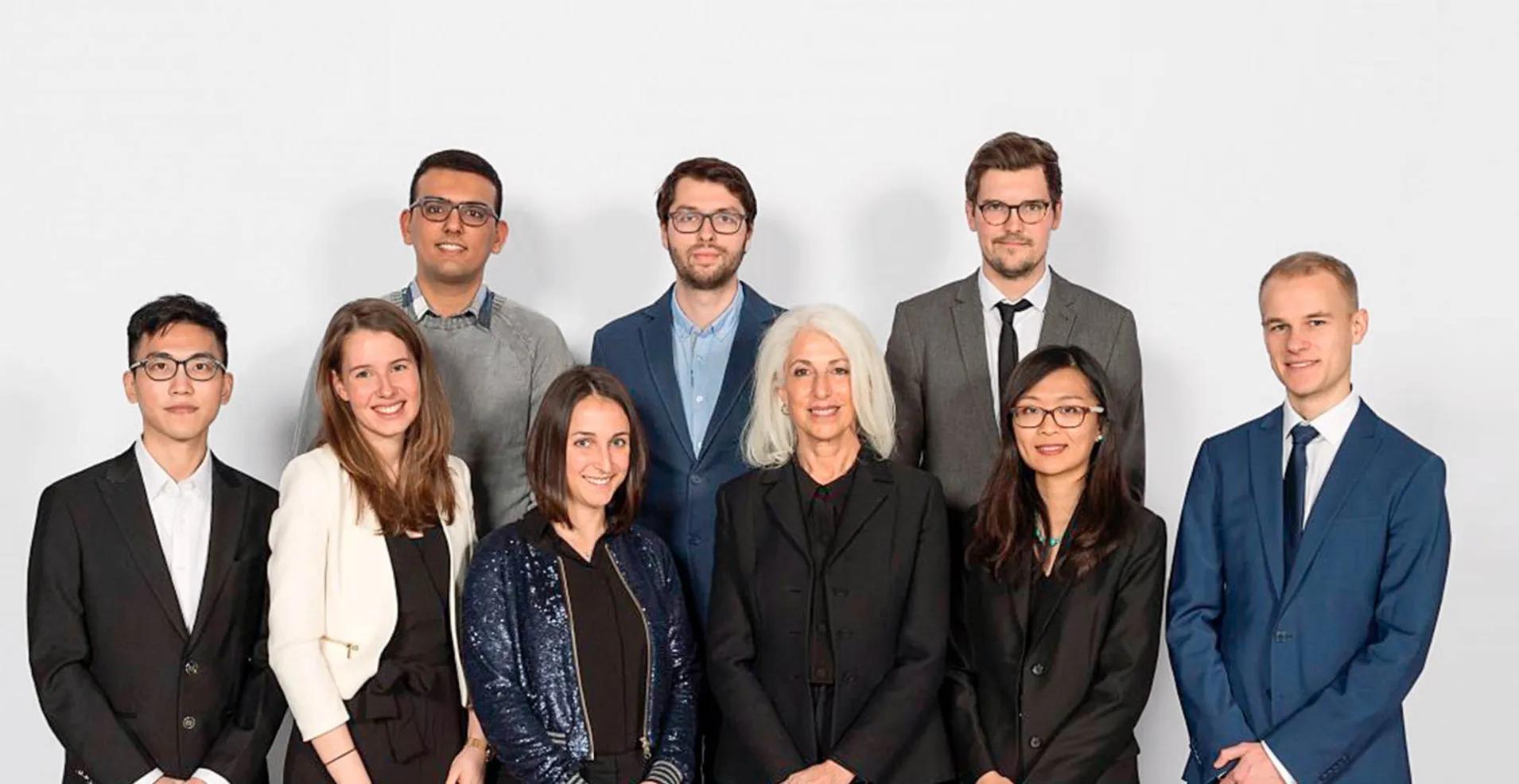
Support for young people and upcoming talents
Every year, the Hans Hörmann Foundation supports talented, high-achieving students at the Technical University of Munich as part of the Scholarship for Germany scheme. Scholarships are also awarded to doctoral students.
“Supporting young people is extremely important to us. We want to enable talented young people to flourish above and beyond their studies and obtain an insight into the diversity of the industry and the HÖRMANN Group at an early stage,” explains Elizabeth Hörmann, Chair of the Hans Hörmann Foundation.
For HÖRMANN as a family-owned company, for our company founder Hans Hörmann and for the Hörmann shareholder family, corporate responsibility goes hand in hand with social responsibility. We strive to create added value for society as a whole.
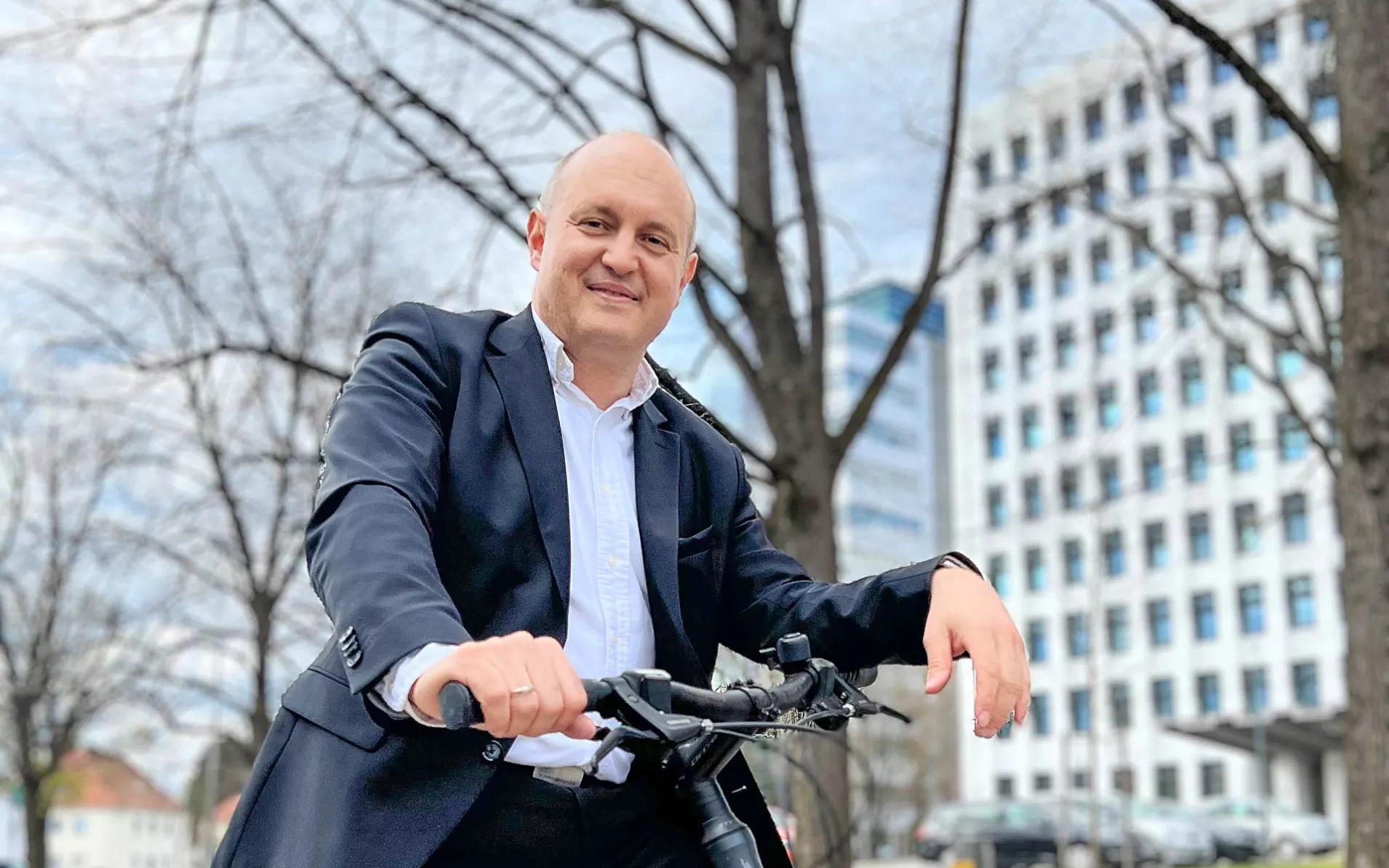
Benefits for our employees
Benefits for cycling to work
Cycling is good for the climate and good for your health. And benefits increase employee satisfaction and make work more fun. HÖRMANN is offering one such benefit in partnership with www.jobrad.org: Employees can select the bicycle of their choice from a range of selected dealers.
The employer then leases the bicycle and provides it to the employee to use whenever and however they want: to travel to work, in their everyday lives, and on holiday. This saves them money compared with buying a bicycle the usual way. Vedran Beslač, Senior Legal Counsel at HÖRMANN Industries GmbH, is full of enthusiasm:
»I intend to cycle more in future, so the offer from the HR department came at just the right time for me. I have already gone on my first rides. Cycling to work is a bit too much for me right now, since I live a few dozen kilometres away – but who knows, it might well become an option as I get fitter.«
Vedran Beslač
Senior Legal Counsel in der HÖRMANN Industries GmbH
The hot topics at the Group
Daniela Heger, industrial designer at H.RMANN Vehicle Engineering GmbH: “I never fail to be impressed by the diversity within the HÖRMANN Group. The ‘mittendrin’ employee magazine regularly showcases the different companies and provides insights into their flagship projects, working environment and culture. I especially enjoy the introduction, which neatly summarises the current situation and the hot topics at the Group and gives you the good feeling of belonging.”
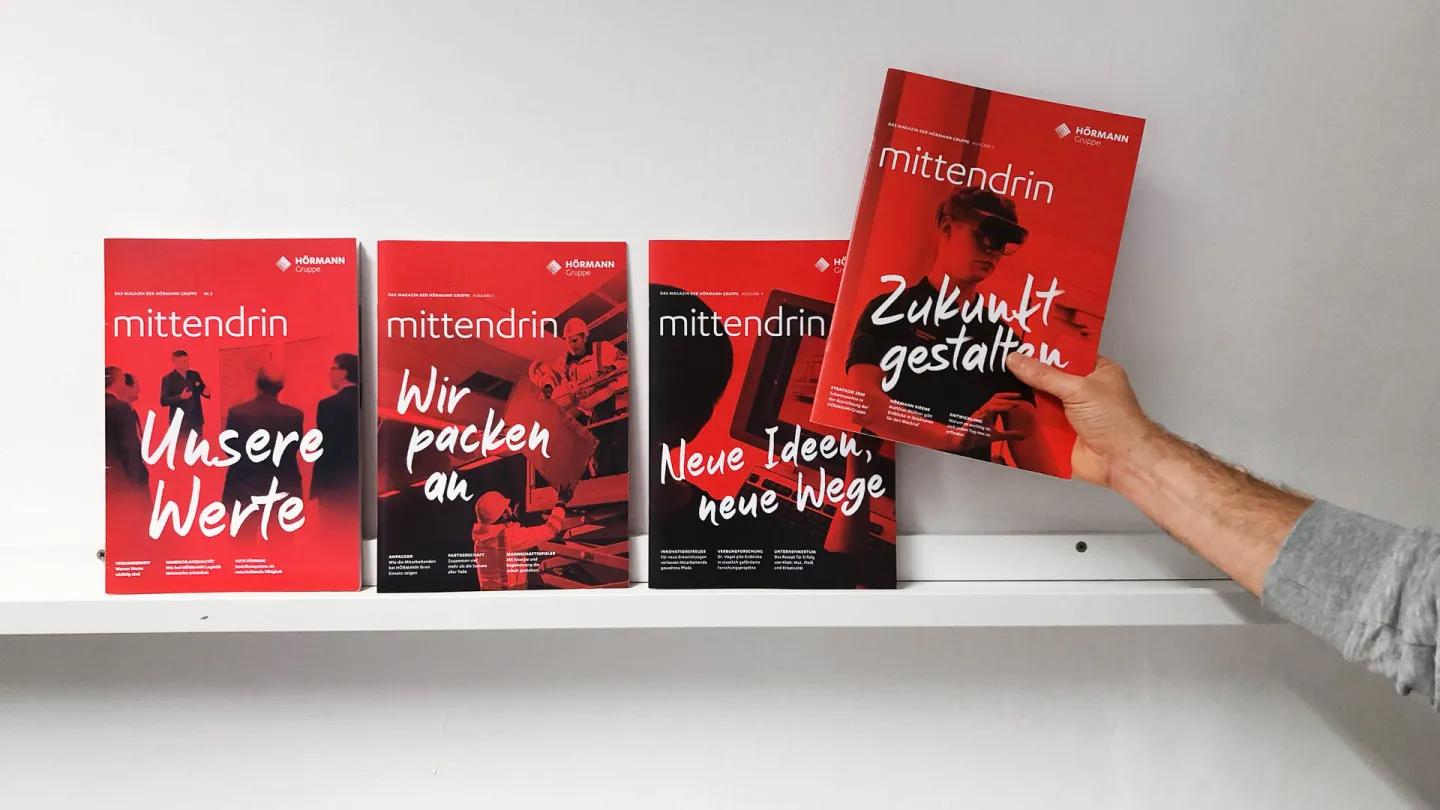
Thinking about tomorrow today
“As an employer, we are also responsible for ensuring our employees’ pension provision,” says Johann Schmid-Davis, CFO of the HÖRMANN Group. The HÖRMANN Group offers its employees a modern, pioneering system: the HÖRMANN pension. All employees can voluntarily contribute portions of their salary to a separate pension scheme, saving them taxes and social security contributions while also allowing them to benefit from an extremely generous employer subsidy. Johann Schmid-Davis: “By providing a strong company pension scheme, we are doing our bit to ensure that our employees can look to the future without worry.”
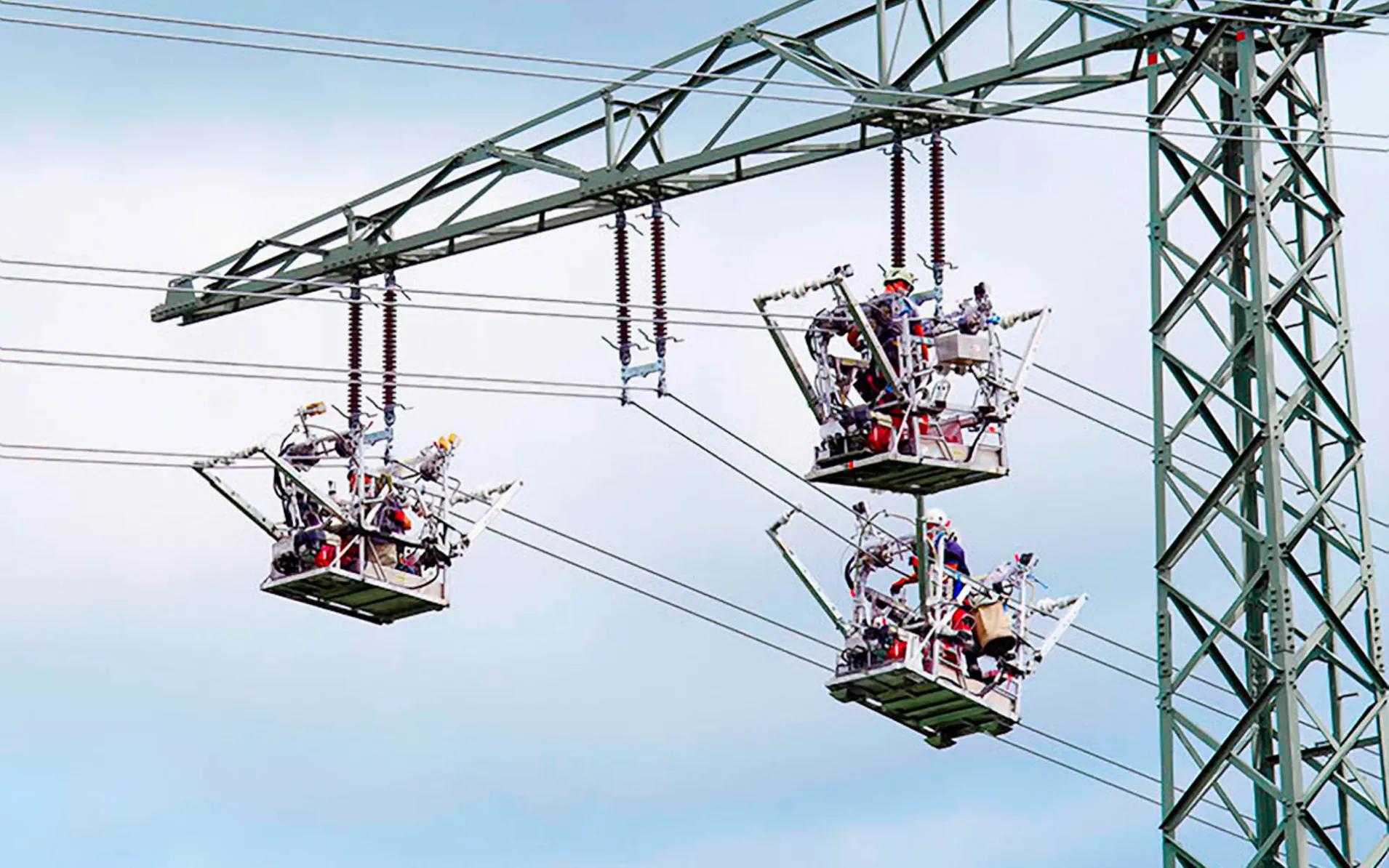
Occupational health and safety
Working safely in a dangerous environment
“Fortunately, we have never had a workplace accident with serious consequences for anyone’s health – even though our employees do spend time in dangerous environments. For example, some of them work on pylons or at great heights, while others work on the railway track bed. Protecting our employees is our top priority!” These are the words of Johannes Antoni, Managing Director of HÖRMANN Kommunikation & Netze GmbH. The certified work safety management system, which is also used at the company’s nine branches, controls all processes in order to ensure the highest possible degree of occupational safety. The company has a dedicated safety expert to assist the management in fulfilling its responsibilities in this area. Johannes Antoni adds: “Every year, we organise an occupational safety week and health days. Regular training, continuous awareness of potential dangers and the systematic analysis of incidents, including the implementation of protective measures, are the key to preventing accidents. Every branch, every task and every construction site has its own specific requirements and hazardous situations and requires the appropriate occupational safety measures.”
The highest standards of health management
Over the past two years, the key topics for Bernd Jermis have been the COVID-19 pandemic, protecting more than 600 employees and maintaining the factory’s production capability. He is responsible for occupational safety at HÖRMANN Automotive Gustavsburg GmbH – and thus also for health protection. “We had some cases of infection, but no major outbreaks,” he notes with relief. Working in close cooperation with management, he and his colleagues at the plant adopted a “safety first” approach right from the start.
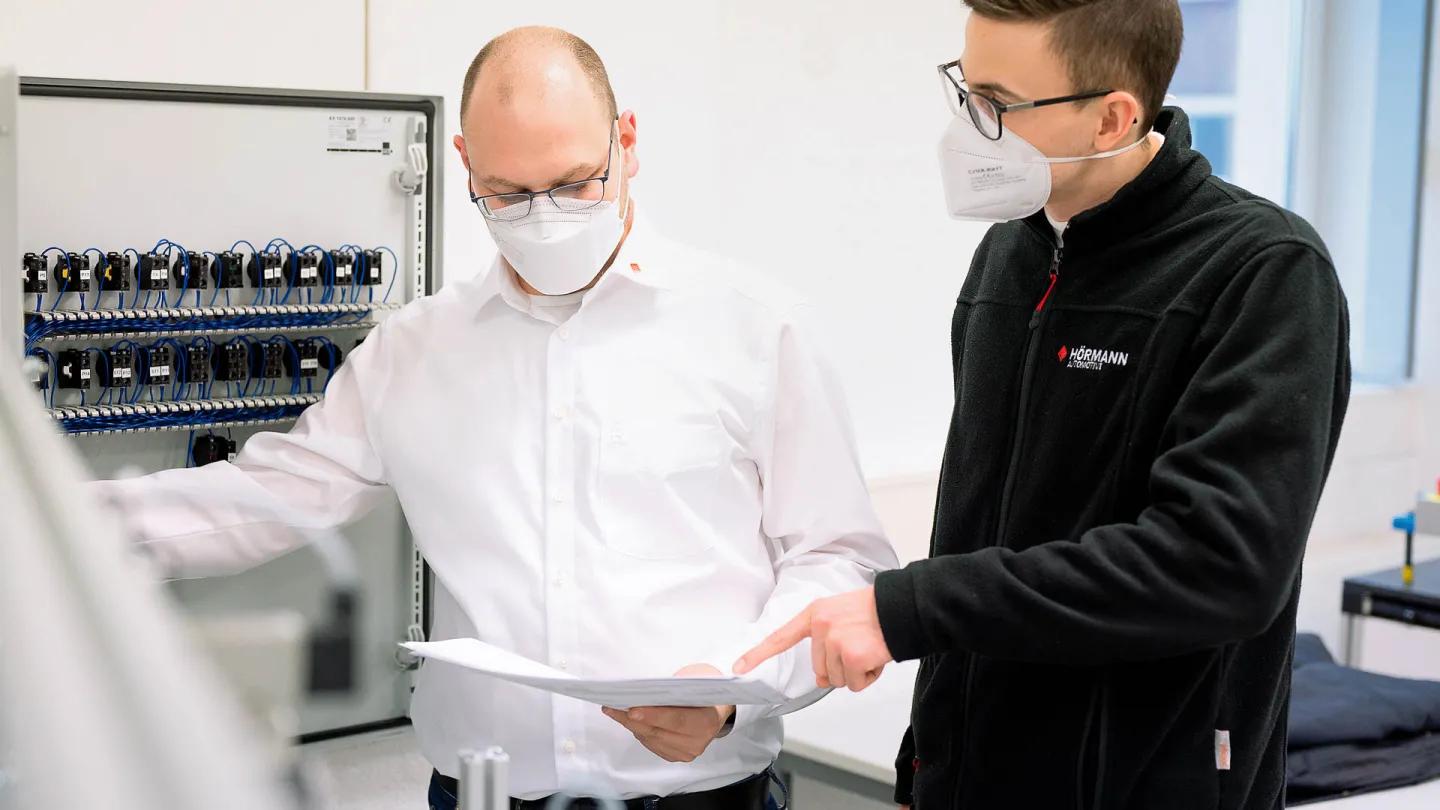
A test facility was quickly established
At the onset of the pandemic, the occupational safety team at the Gustavsburg plant provided employees with high-quality masks that they could also use outside the workplace. A test facility was quickly established and mobile teams were even able to perform tests in the workplace. At the factory gate, a strict checkpoint was set up for all visitors and truck drivers with mandatory testing and, later, mandatory application of the German “3G” rules. A vaccination centre was established at the plant at a very early stage and the necessary vaccines were provided to employees via various special campaigns. Family members were also offered vaccinations. This helped to prevent numerous infections and identify cases as quickly as possible. As Bernd Jermis says: “We achieved our goal. The production capability of the plant was never in danger – thanks to everyone’s efforts.”
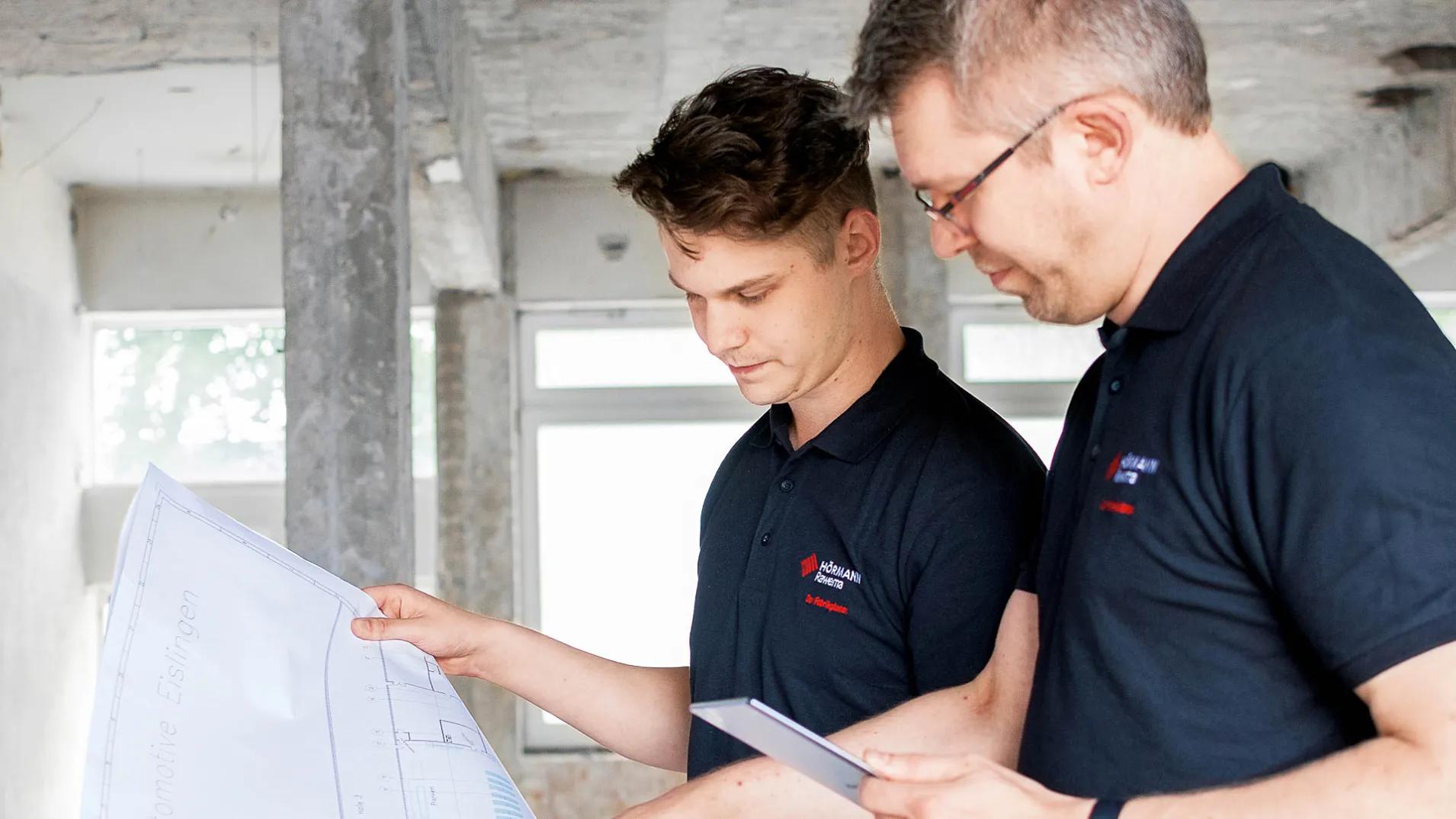
Training and qualifications for the employees of tomorrow
Training and qualifications at HÖRMANN Automotive
When he shows people around the training workshop at HÖRMANN Automotive Eislingen GmbH, Artur Knödlseder loves to point out the different machines at which trainees start learning their trade. “I have been a training instructor for more than 20 years,” he says, adding: “Only ever for boys. But now we have the first two girls training to be construction mechanics.”
In-house training has a long tradition at HÖRMANN.
Trainees are familiarised with different areas of work, allowing them to decide what suits them best in the long term. Our aim is to prepare young people for the specific requirements of the respective trade at an early stage and provide them with valuable skills and qualifications for the future. Although the training vocations vary considerably – from construction mechanics to toolmakers to industrial clerks – all of the trainees learn a great deal, are handed responsibility at a young age, and get used to working independently. “At the same time, however, the whole team is always on hand to assist the trainees with their work and help them with any questions or tasks,” Artur Knödlseder emphasises.
Dual study programme: theory and practice in perfect harmony
The HÖRMANN Group offers students a dual study programme that encompasses both practical training and academic studies. Felix Ullmann has already completed his dual study programme with HÖRMANN Rawema GmbH and now works as a project engineer: “Right from the start, I enjoyed the opportunity to combine hands-on work with theoretical learning.”
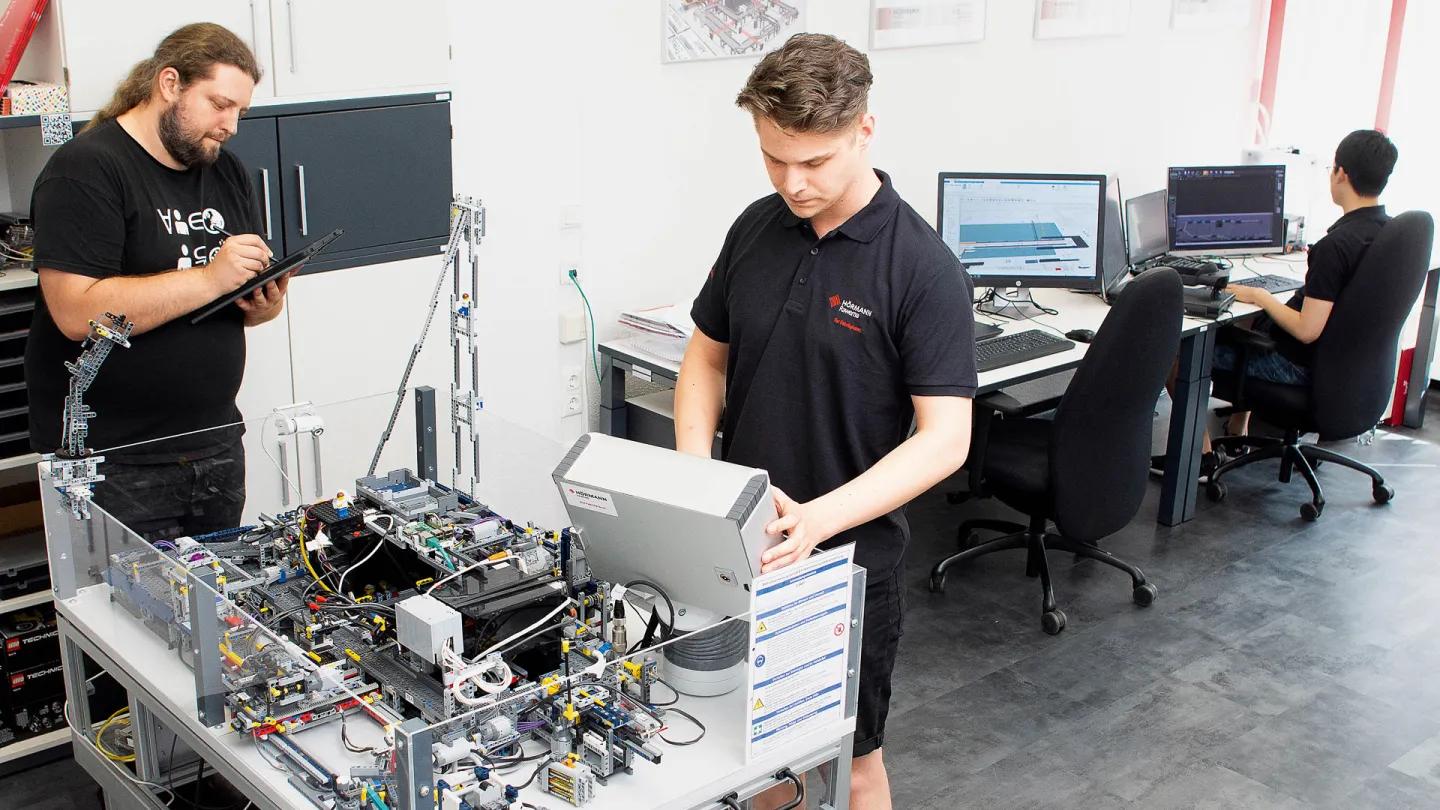
Other students also appreciate the practical experience and the specific insights into the world of work. Benjamin Bielefeld, Managing Director of HÖRMANN Rawema, adds: “Dual study programmes require employers to integrate students into working processes at an early stage, making them the ideal combination of in-house training and external education.” The prospective engineers at HÖRMANN companies such as Automotive, BauPlan and Rawema are quickly made a part of the team – and typically end up staying with the company for the long term. This is hugely advantageous, not least at a time when there is a shortage of engineers.
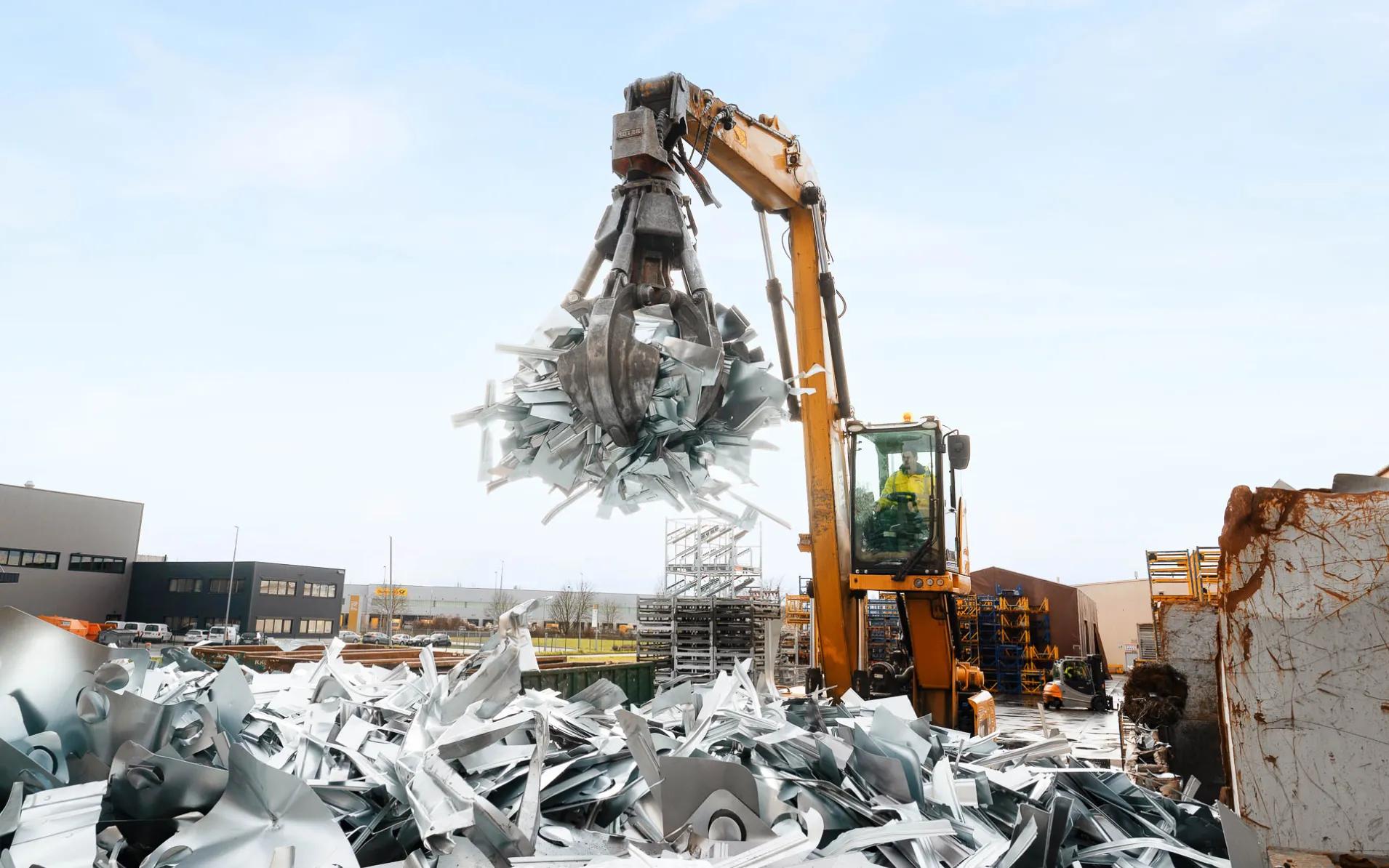
Valuable recycling to conserve natural resources
By definition, scrap is something that gets thrown away. However, scrap metal is a valuable secondary raw material that makes an importantncontribution to conserving natural resources and reducing the energy used in metal processing. “Industry has long been working hard to develop ways of getting the best possible use out of the expensive commodity of steel and generating as little waste as possible,” says Stefan Kuhn, Managing Director of HÖRMANN Automotive Gustavsburg GmbH.
There are different approaches to achieving this: producing less waste by optimising the arrangement of the products to be punched on a board, and investing directly in high-quality recycling.
»Although our Gustavsburg plant processes more than 100,000 tons of steel every year, thus converting a huge quantity of raw materials into valuable components for the commercial vehicle industry, we also do our best to conserve the world’s natural resources through efficient recycling.«
Stefan Kuhn
Managing Director of HÖRMANN Automotive Gustavsburg GmbH
Proper separation is important
Steel is well suited to recycling because it can be easily melted down again. “We know that our scrap is transported to selected recyclers. Steelworks then use the scrap steel as aggregate in new steel products,” says Stefan Kuhn.
To ensure the purity and quality of the new material, it is important that scrap is strictly separated and that no foreign substances find their way into the containers. At the Gustavsburg plant, the waste (or scrap) resulting from the pressing and punching process is collected in containers manually or using conveyor belts – and carefully separated by individual material type.
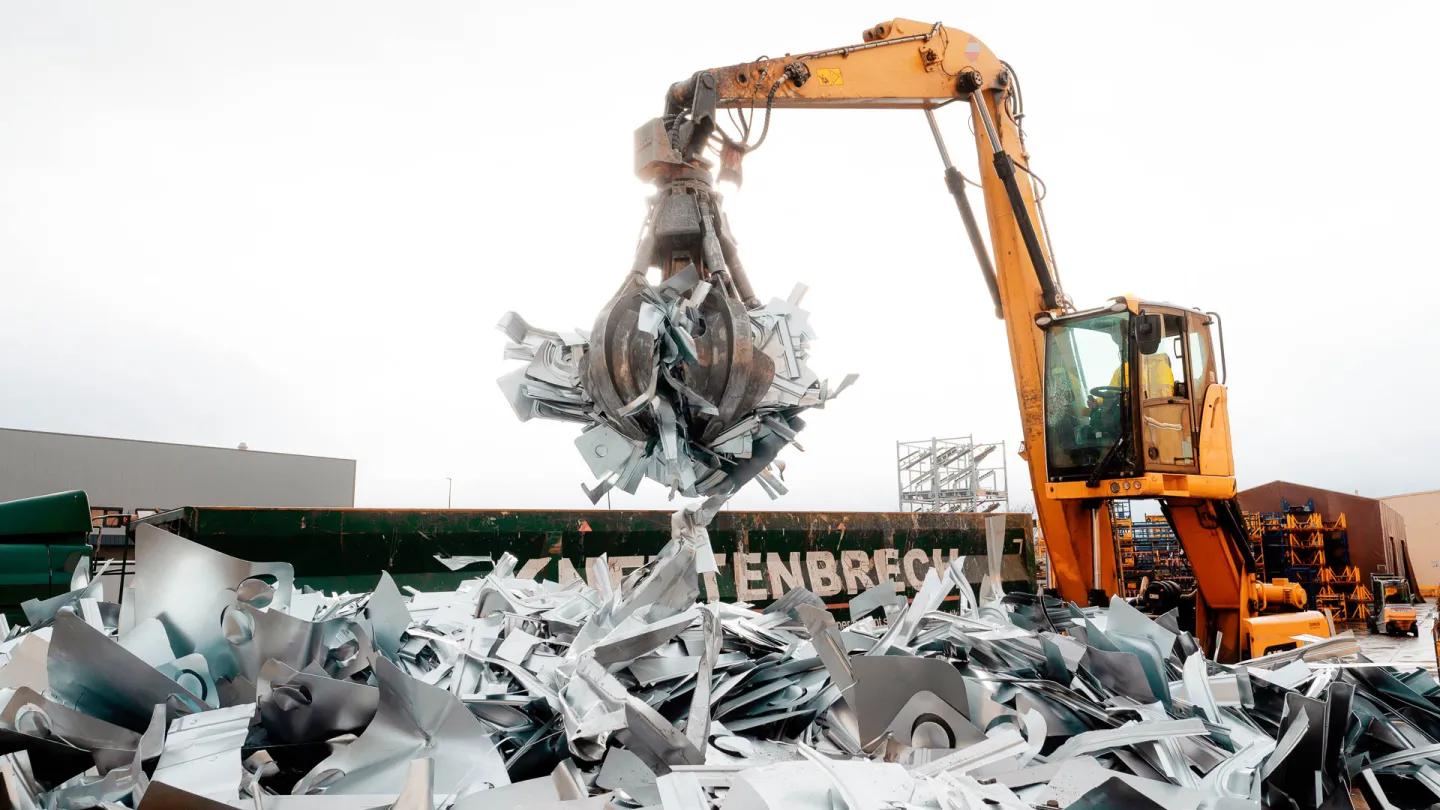